The primary purpose for estimating an improvement curve is to predict the cost of future
production. The prediction is based on the assumption (not always true) that the past is a good
predictor of the future. In terms of the unit improvement curve theory, this assumption means
that the unit cost (hours or dollars) of doubled quantities will continue to decrease by the same
constant percentage.
Using a graph, you can predict future costs by drawing a line-of-best-fit through the historical
data graphed on log-log paper and extending it through the unit for which you wish to make a
cost estimate. Estimate cost using the Y value (cost) at the point were the two lines intersect.
For example, suppose we had the following unit cost data:
Unit Number Hours
1 3,000
2 2,400
4 1,920
8 1,536
Plotting the data on log-log paper, you will observe a straight line with an 80 percent slope.
If you extend the line-of-best-fit to Unit #100, you can estimate the cost of Unit #100. As you
can see from the graph, the extended line reveals an estimated cost of approximately 680 hours
for Unit #100.
7.3 Analyzing Improvement Using Lot Data and Unit Theory
Accounting System Data
Use of the improvement curve is dependent on available cost data. The relevant accounting or
statistical record system must be designed to make relevant data available for analysis. Costs,
such as labor-hours per unit or dollars per unit, must be identified with the unit of product.
NOTE: It is preferable to use labor-hours rather than dollars since the dollars contain an
additional variable, the effect of inflation or deflation, which the labor-hours do not contain
.
Typically accounting systems do not record the cost of individual units. If the firm uses a joborder cost accounting, costs are accumulated on the job order in which the number of units
completed are specified and costs are cut-off at the completion of the units. Process cost
accounting also yields costs identified with end-item units. In this case, however, the costs are
usually assigned to equivalent units produced over a period of time rather than actual units.
Average Unit Cost
To use unit improvement curve theory, you must be able to estimate the cost of a particular unit.
Given lot or period costs, the only unit cost that we know is the average cost for the lot or period.
However, we have a method for using average costs in improvement curve analysis.
For example, given the following data, we must be able to estimate the cost of an additional 40
units.
Lot Number Lot Size
(Units)
Lot Total
Labor-Hours
(Cost)
Lot Average
Labor Hours
(Cost)
1 6 40,800 6,800
2 9 40,500 4,500
3 15 52,500 3,500
Calculating a Lot Plot Point for Graphic Analysis
To graph the lot average unit cost, we must select a corresponding unit number. If we assume
that costs go down during the lot, the average cost should occur at the middle of the lot – the lot
mid-point. One problem is that the True Lot Mid-Point (the unit where the average cost is
incurred) depends on the slope of the improvement curve. Unfortunately, the slope of the curve
also depends on the placement of the Lot Mid-Point. The iterative process required to calculate
the True Lot Mid-Point for each lot is too cumbersome for manual computation. As a result, we
use the following rules of thumb for graphic analysis:
⢠For All Lots After The First Lot, calculate the lot mid-point by dividing the number
of units in the lot by two . Then add the resulting number to all the units produced prior
to the lot to determine where the unit falls in the continuing improvement curve.
For example, what would be the plot point for a lot made up of units 91 through 100. There are
10 units in the lot, so the middle of the lot would be 5 (10 2 = 5). Adding 5 to the 90 units
produced prior to the lot, we find that the plot point would be 95.
⢠For a First Lot of Less Than 10, follow the same procedure that you follow for all lots
after the first lot. Of course, the lot plot point will equal the lot mid-point because no
units will have been produced prior to the first lot.
⢠For a First Lot of 10 or More, calculate the lot mid-point by dividing the number of
units in the lot by three . This adjustment is necessary to compensate for the rapid
decline in cost that takes place in the first lot of production.
Given the data above, use a table similar to the following, to calculate the necessary lot plot
points and lot average hours:
Lot No. Lot Size Cumulative
Units
Lot MidPoint
Lot Plot Point
1 6 6 3.0 3.0
2 9 15 4.5 10.5
3 15 30 7.5 22.5
You can then use this information to estimate the cost of lots that have
not yet been produced. For example, suppose you wanted to estimate the
cost of a Lot #4 of 40 units to be produced after the 40 units described
above. The final row of the table would be:
4 40 70 20 50
For this example, the lot plot point for Lot #4 would be at Unit #50. You
would estimate the average unit cost for the lot using the cost of Unit
50.
Combining Lot Plot Point and Average Unit Cost Calculation
You can combine the calculation for the lot average unit cost and the lot plot point into a single
table, as shown below:
Lot
No.
Lot
Size
Cumulative
Units
Lot MidPoint
Lot
Plot
Point
Lot
Average
Hours
Lot
Total
Hours
1 6 6 3.0 3.0 6,800 40,800
2 9 15 4.5 10.5 4,500 40,500
3 15 30 7.5 22.5 3,500 52,500
4 40 70 20.0 50.0
Plotting Data on a Log-Log Graph
Plot the average lot cost data (Y) at the corresponding lot plot point (X) on log-log paper and for
an improvement curve. Extend the improvement curve through Unit #50, the lot plot point for
Lot #4.
On the Y axis, the lot average cost at Unit #50 is approximately 2,700 labor hours. With this
information, you can estimate the cost of Lot #4 at 108,000 labor hours (i.e., 2,700 labor hours x
40 units).
7.4 Fitting a Unit Curve
General Points to Consider
Throughout this chapter, we have assumed that all data fit a perfectly straight line.
Unfortunately, most data do not fall exactly on a straight line. You need to be able to identify a
trend and fit data to that trend. You can visually fit a line using graphic analysis, but most linesof-best-fit are developed using regression analysis.
Whatever method of analysis you use to fit an improvement curve, if a data point is a significant
distance away from the trend set by other data points, look into the cause of the deviation. If your
analysis indicates that the data point is not comparable with the rest of the data for some reason,
consider adjusting or eliminating the data point from your analysis. However, never eliminate a
data point from your analysis simply because it does not fit the apparent trend set by the
remaining data.
Graphic Analysis
When visually fitting a straight line, graph the data then draw the line to minimize the distance
between the straight line and the data points. Normally, you should give more weight to the
larger lots as you fit the straight line.
When fitting a straight line on ordinary graph paper, you know that the line-of-best-fit must go
through the average of the X values ( ) and the average of the Y values ( ). When fitting a line-ofbest-fit through improvement curve data on log-log paper, you have no similar fixed reference
point. Without this fixed reference point, even skilled analysts can arrive at very different
lines.
Regression Analysis
Normally, you can obtain more accurate results using regression analysis and a log-log
transformation. Using the logarithmic values of X and Y instead of the actual values, the
equation of the unit improvement curve (Y = AXB) becomes:
Log Y = Log A + B(Log X)
The new equation describes a straight line (Y = A + BX) relationship. After this transformation,
you can use regression analysis to fit a straight line to the data.
Improvement curve regression analysis programs differ in several ways including:
⢠Use of True Lot Mid-Point.
In addition to the accuracy gained from using regression analysis, most improvement curve
programs use the true lot mid-point rather than the rule-of-thumb calculations described earlier in
this section for graphic analysis. The greatest effect of using the true lot mid-point is in the first
lot. Examples of the differences between the rule-of-thumb and true lot mid-points are depicted
in the following table:
Selected First Lot Mid-Points
True-Lot Mid-Points
Units in
First Lot
Rule-ofThumb
70%
Curve
80%
Curve
90%
Curve
2 1.00 1.37 1.39 1.4
10 3.33 3.95 4.17 4.36
100 33.33 28.65 32.36 35.43
1,000 333.33 258.15 304.43 340.67
10,000 3333.33 2,495.48 3,002.85 3,384.18
Differences in calculating the lot mid-point will affect the results of the improvement curve
analysis by the placement of the data points for analysis.
⢠Method of Regression.
Not all improvement curve analysis programs use the same mathematical model for regression
analysis. For example, some analysis programs assign a weight to each lot based on the lot size,
while others do not. Software using unweighted regression considers all lots (large and small)
equally. When weights are assigned to each lot based on lot size, larger lots receive more
analysis consideration than smaller lots.
⢠Measures of Fit.
o Regardless of the regression model used to develop the line-of-best-fit, virtually
all regression analysis software will provide measures of the line’s goodness of fit.
o The primary goodness of fit measure is the coefficient of determination (r 2 ) for
the equation. As described in the chapter on “Using Regression Analysis,” the
coefficient of determination indicates the portion of variation in Y is explained by
the regression line (e.g., an r 2 of .94 indicates that 94 percent of the variation in Y
is explained by the relationship between X and Y).
o Many improvement curve analysis programs also provide the T-test for
significance of the regression equation.
⢠Graphic Analysis Capability.
Many regression analysis programs provide a capability to graph the data and the regression line.
For most analysts, this display is one of the strongest tools for identifying anomalies in the data
that affect the value of the regression analysis as an estimating tool.
7.5 Estimating Using Unit Improvement Curve Tables
Estimating Choices
Once the cost of Unit #1, in hours or dollars, and the slope of the improvement curve have been
established, we can develop estimates of future costs in several ways. You could graph the data
on log-log paper and read your estimates from the graph. You could substitute the values into the
improvement curve equation. Many analysts use a third choice, improvement curve tables.
Improvement Curve Tables
Improvement curve tables are an expansion of the X B portion of the basic unit improvement
curve equation, Y = A X B . The result is recorded as a decimal fraction, which is typically
calculated to six or eight decimal places. There is a different table value for each unit and slope.
Below is an illustration of a partial improvement curve table.
Partial Improvement Curve Table
79 Percent 80 Percent 81 Percent
Unit Cum Total Unit Cum Total Unit Cum Total Unit
1 1.000000 1.000000 1.000000 1.000000 1.000000 1.000000
2 1.790000 0.790000 1.800000 0.800000 1.810000 0.810000
3 2.478245 0.688245 2.502104 0.702104 2.526065 0.716065
4 3.102345 0.624100 3.142104 0.640000 3.182165 0.656100
5 3.680837 0.578492 3.737741 0.595637 3.795233 0.613068
6 4.224550 0.543713 4.299424 0.561683 4.375245 0.580012
7 4.740494 0.515944 4.833914 0.534490 4.928703 0.553458
8 5.233533 0.493039 5.345914 0.512000 5.460144 0.531441
9 5.707214 0.473681 5.838864 0.492950 5.972892 0.512748
10 6.164223 0.457009 6.315374 0.476510 6.469477 0.496585
11 6.606656 0.442433 6.777485 0.462111 6.951880 0.482403
12 7.036189 0.429533 7.226831 0.449346 7.421690 0.469810
13 7.454188 0.417999 7.664747 0.437916 7.880206 0.458516
14 7.861784 0.407596 8.092339 0.427592 8.328507 0.448301
15 8.259928 0.398144 8.510538 0.418199 8.767503 0.438996
16 8.649429 0.389501 8.920138 0.409600 9.197970 0.430467
17 9.030982 0.381553 9.321821 0.401683 9.620576 0.422606
18 9.405190 0.374208 9.716181 0.394360 10.035902 0.415326
19 9.772580 0.367390 10.103736 0.387555 10.444457 0.408555
20 10.133617 0.361037 10.484944 0.381208 10.846691 0.402234
21 10.488713 0.355096 10.860211 0.375267 11.243003 0.396312
22 10.838235 0.349522 11.229900 0.369689 11.633750 0.390747
23 11.182513 0.344278 11.594336 0.364436 12.019252 0.385502
24 11.521844 0.339331 11.953813 0.359477 12.399798 0.380546
25 11.856497 0.334653 12.308597 0.354784 12.775651 0.375853
26 12.186716 0.330219 12.658929 0.350332 13.147049 0.371398
27 12.512724 0.326008 13.005031 0.346102 13.514210 0.367161
28 12.834725 0.322001 13.347104 0.342073 13.877334 0.363124
29 13.152906 0.318181 13.685335 0.338231 14.236605 0.359271
30 13.467440 0.314534 14.019894 0.334559 14.592192 0.355587
Unit Estimate.
To estimate the price or cost for a specific unit, you can simply multiply the cost of Unit #1 by
the appropriate unit factor for the desired unit and slope.
Where:
Y U = T 1 x F U
Y U = Unit cost estimate
T 1 = Theoretical cost of Unit #1
F U = Unit cost factor for the unit.
For example, if Unit #1 is 2,000 labor hours, what would be your estimate for Unit #20 if
production is expected to follow an 80 percent improvement curve? The table value for Unit #20
and an 80 percent slope is .381208. The estimate would be 762.4 labor hours, calculated as
follows:
Y U = T 1 x F U
= 2,000 labor hours x .381208
= 762.4 hours
We need to do the same thing for Lot Data:
Y L = (T 1 x F C2 ) – (T 1 x F C1 )
Where:
Y L = Lot cost estimate
T 1 = Theoretical cost of Unit #1
F C2 = Cumulative cost factor for all production through the proposed lot
F C1 = Cumulative cost factor for all production prior to the proposed lot
For ease of calculation, this equation may be rewritten as:
Y L = T 1 (F C2 – F C1 )
For example, if Unit #1 is 4,000 labor hours and the improvement curve slope is 80 percent, what
would be your estimate for Units #15 to #25? Your estimate should be 15,192.24 labor hours,
calculated as follows:
YL = T1(FC2 – FC1)
= 4,000 (12.308597 – 8.092339)
= 4,000 (4.216258)
= 16,865.032 (rounded to 16,865 labor hours)
7.6 Identifying Issues and Concerns
Questions to Consider in Analysis
As you perform price or cost analysis, consider the issues and concerns identified in this section,
whenever you use an improvement curve.
⢠Is improvement curve analysis used when the contract effort involves:
⢠A significant amount of manual labor in the contract?
⢠Uninterrupted production?
⢠Production of complex items?
⢠No major technological change?
⢠Or should involve, continuous pressure to improve?
⢠Does the documentation to support the use of the improvement curve include:
o A statement describing the improvement curve theory used in developing the
estimate?
o A summary of related cost data for the product being purchased and any similar
products?
o A description of how available data were used in estimating the theoretical cost of
Unit #1 and the slope of the curve?
o A statement on how the improvement curve estimate was used in price or cost
analysis?
Like CERs, improvement curves are a form of comparison estimate. Unless you are satisfied that
the historical data provide a valid base for the use of an improvement curve, estimates based on
the curve should be suspect.
⢠Was improvement curve theory properly applied to the available data?
Verify the application of the improvement curve to the data available. Remember that different
improvement curve models will produce different results.
For instance, you may find that a unit curve will provide more reasonable results than a
cumulative average curve provided by an offeror. Examine the results of both curves when an
offeror proposes using a cumulative average curve, because cumulative average curves often
conceal significant fluctuations in per unit labor hours.
⢠Did any improvement curve analysis isolate costs associated with contract changes
and production interruptions?
Changes and production interruptions will both have a disruptive effect on improvement. If their
effects are not identified and considered in analysis, improvement curve estimates will typically
underestimate actual requirements. Random fluctuations around an improvement curve line-ofbest-fit should be expected. However, if costs increase or decrease dramatically, you should
suspect that the actual costs have been affected by a contract change or a break in production.
When you suspect that actual costs are affected by a contract change or break in production,
contact the cognizant auditor and Government technical personnel for assistance in your
analysis.
On the other hand, an offeror might overstate the impact of an interruption in productioncontending that the interruption has been so long that it will have to start from scratch. However,
impovements in unit costs result in part from such factors as better product design, tooling, work
methods, and work layout. If these were properly documented, some of the improvement should
carry over to the new effort-regardless of the length of the interruption or turnover of personnel.
⢠Does the improvement curve analysis project continued improvement?
Occasionally, an offeror will propose “negative learning.” In other words, as more units are
produced, the cost per unit increases. Do not accept the negative learning argument. If something
has significantly changed, consider starting a new curve with a new first unit value and slope.
⢠Does the improvement curve estimate include the costs of rework and repair?
The effort for rework and repair may or may not be included in the costs projected with the
improvement curve. Therefore, you need to determine if these costs are included in the projected
costs before allowing any add-on factors for rework or repair.
⢠8.0 – Chapter Introduction
⢠8.1 – Identifying Situations For Use
⢠8.2 – Identifying Elements Of A Labor Standard
⢠8.3 – Measuring And Projecting Operation Efficiency
⢠8.4 – Identifying Issues And Concerns
8.0 – Chapter Introduction
In this chapter, you will learn about work measurement concepts and their application to cost
analysis.
Work Measurement . Work Measurement involves the use of labor standards to measure and
control the time required to perform a particular task or group of tasks. Most often labor
standards are developed and applied in manufacturing operations; however labor standards can
be used in estimating and managing the cost of a vast variety of activities including engineering
drafting, clerical administration, and janitorial services.
Work Measurement System . A Work Measurement System is a management system designed to:
⢠Analyze the touch labor content of an operation;
⢠Establish labor standards for that operation;
⢠Measure and analyze variances from those standards; and
⢠Continuously improve both the operation and the labor standards used in that operation.
Work Measurement System Plan . A Work Measurement System Plan is the firm’s program for
implementing, operating, and maintaining work measurement in its operations. As a minimum,
the plan should provide guidance on:
⢠Establishing and maintaining standard accuracy;
⢠Conducting engineering analyses to improve operations;
⢠Revising standards and related system data; and
⢠Using labor standards as an input to budgeting, estimating, production planning, and
performance evaluation.
Labor Standard Types . A labor standard is a measure of the time it should take for a qualified
worker to perform a particular operation. Labor standards are commonly grouped into two types:
⢠Engineered standards are developed using recognized principles of industrial
engineering and work measurement. The standards developed define the time necessary
for a qualified worker, working at a pace ordinarily used, under capable supervision, and
experiencing normal fatigue and delays, to do a defined amount of work of specified
quality when following the prescribed method. As a result, you can use engineered
standards to examine contractor estimated labor hours and to identify any projected
contractor variances from that estimate.
⢠Non-engineered standards are developed using the best information available without
performing the detailed analysis required to develop engineered standards. Historical
costs are commonly used standards that typically measure the hours that have been
required to complete a task rather than the hours that should be required.
Estimate of Efficient Operation Cost . Standards provide information on what it should cost to
complete an operation or series of operations in product production. Instead of applying pressure
to improve in all areas, managers can use this information to identify areas requiring particular
management emphasis. The Acquisition Team can use that same information to identify
inefficient operations for close scrutiny during contract negotiations.
⢠The log-log graph below presents a line-of-best-fit developed using actual labor-hour
history. Note that this line follows the form of the improvement curve. Without labor
standards, the firm and the Government would likely project the improvement curve to
estimate the labor hours required to produce future units.
⢠Labor standards provide additional information that can be used in estimate development
and analysis. The vertical distance between the labor-hour history and the labor standard
represents the variance from the standard. Some of that variance may be related to
inefficiencies that cannot be resolved. However, all elements should be targeted for
identification and analysis. Key elements include:
o Technical factors (e.g., manufacturing coordination, engineering design changes,
fit problems, design errors, operation sheet errors, tooling errors, work sequence
errors, and engineering liaison problems).
o Logistics (e.g., incorrect hardware and parts shortages).
o Miscellaneous factors (e.g., unusual working conditions, excessive overtime, and
excessive fatigue).
o Worker learning (e.g., familiarity with processes and methods).
⢠Variance analysis should identify, categorize, and develop plans to control all variances
from standard. Plans will typically concentrate on the operations with the largest
variances from standard, because these operations present the greatest opportunity for
cost reduction.
Updating Standards . Standards cannot be set and forgotten. Process improvement is one of the
central elements of an effective Work Measurement System. As methods improve, the associated
labor standards must be updated.
Standards changes will affect the estimating value of all the data based on those standards. For
example, some variance analyses may remain valid while other analyses will be rendered
meaningless as a result of the change. The system must assure that valid analyses are retained for
continued utilization. At the same time, the system must also assure that meaningless data are not
misused.
8.1 – Identifying Situations For Use
General Situations . Contractors should consider the use of labor standards whenever contractor
employees will be performing the same tasks repetitively over an extended period of time. Labor
standard development requires extensive detailed effort. The time and cost required for standards
development are prohibitive unless the task will be performed repetitively. On the other hand,
when an operation will be performed repetitively, the cost visibility provided by labor standards
permits detailed cost evaluation and control that can result in significant savings to the
Government. To be of real value, labor standards must be considered in making key management
decisions (e.g., budgeting, estimating, production planning, and performance evaluation).
8.2 Identifying Elements Of A Labor Standard
Key Elements . As a contracting officer, it is likely that you will never be required to develop a
labor standard. However, you may be called upon to negotiate a contract price based, in part, on
labor standards. Therefore, you should know the elements of a standard and how they are
developed.
The figure below depicts some of the factors that should be considered in each element.
Leveled Time . Leveled time is the time that a worker of average skill, making an average effort,
under average conditions, would take to complete the required task. There are a variety of
techniques used in leveled time development, but the four used most commonly are:
⢠Time Study. In performing a time study, industrial engineers (or other labor analysts)
time the effort required to perform a defined task. While it may sound simple, this is a
complex process that requires special training and experience. To perform a time study,
the analyst must:
o Clearly define and document the work design, including the best design of the
work place, tools, tasks, and subtasks.
o Select a person to be timed. The person selected should be receptive to being
timed, experienced in the work methods being used, and familiar with the tasks
and subtasks of the work design.
o Observe and record the time that the selected worker requires to perform each of
the subtasks in the work design. Several observations are required to average out
random variations and assure that all elements of the work have been considered.
The number of observations required will increase as the confidence level desired
by the analyst increases and as the variability between observed times increases.
o Assign a pace rating based on an evaluation of how the ability and effort of the
worker being timed compares with those of an average worker. Using the pace
ratings, the analyst converts observed times into a leveled time for the subtask.
o Total subtask times to develop a leveled time for the entire task.
⢠Predetermined Leveled Times. Instead of using time study to develop a leveled time,
the analyst can use predetermined leveled times (also called predetermined standards or
basic motion standard data). Predetermined leveled times are established for basic body
motions, such as reach, move, turn, grasp, position, release, disengage, and apply
pressure. The analyst may obtain them from published standards in tabular or electronic
forms, or the firm may develop its own. To use predetermined leveled times, the analyst
must:
o Clearly define and document the work design, including the best design of the
work place, tools, tasks, and subtasks.
o Select and document the source of the predetermined leveled times.
o Identify and document the basic body motions involved in performing each
subtask. Motions for each hand must be specifically identified. The need for
precise measurement of complex body motions for each job element may make
this method of leveled time development inappropriate for complex tasks with
long performance cycle times.
o Assign times to the body motions required to complete each subtask and total
assigned times to develop a leveled time for the subtask. Documentation should
demonstrate that the accuracy of the original data base has not been compromised
in application or standard development.
o Total subtask times to develop a leveled time for the entire task.
⢠Standard Time Data. Standard time data (or elemental standard data) are developed for
groups of motions that are commonly performed together, such as drilling a hole or
painting a square foot of surface area. Standard time data can be developed using time
studies or predetermined leveled times. After development, the analyst can use the
standard time data instead of developing an estimate for the group of motions each time
they occur.
o Typically, the use of standard time data improves accuracy because the standard
deviations for groups of motions tend to be smaller than those for individual basic
motions. In addition, their use speeds standard development by reducing the
number of calculations required.
o Estimate development using standard time data is much like using predetermined
leveled times except that groups of motions are estimated as a single element
instead of individual body motions.
⢠Work Sampling. Work sampling is commonly used to develop non-engineered
standards. It cannot be used alone to develop engineered standards. However, it can be
used to supplement or check standard development by more the definitive techniques
described above. For example, it can be used to determine job content and assess
productive vs. nonproductive time.
o In work sampling, analysis is based on a large number of random, rather than
continuous observations. Estimates are based the proportion of time spent by one
or more persons on a given activity. This is useful for jobs with irregular
components that vary in the amount of time per unit of output.
o To use work sampling in standard development, the analyst must:
ï§ Identify and define activities involved in the work (through discussions
with the workers and preliminary observations).
ï§ Develop the method(s) for observing and recording activities.
ï§ Determine the sampling strategy (e.g., stratified) and number of
observations (by time and place).
ï§ Record observed activities during each period.
ï§ Consolidate and analyze the data.
ï§ Use the data collected to develop nonengineered standards or to
supplement development of engineered standards.
PF&D Allowance . After the leveled time is developed, estimators must consider a personal,
fatigue, and delay (PF&D) allowance. Be careful when contractors use predetermined time
systems. Some predetermined time systems include a partial or complete allowance for PF&D. If
the contractor uses such standards, additional PF&D consideration may not be appropriate.
Contractor work measurement policies and procedures should provide the detailed rationale used
for applying PF&D allowances. Each allowance should be identified and quantified. Total PF&D
allowances typically total 15 percent. However, allowances may be higher or lower depending
on the nature of the work and related working conditions. For example, strenuous work in an
extremely hot environment would typically merit a higher PF&D allowance than light labor
performed in an air conditioned room.
Personal Allowance. A personal allowance considers time for a worker to take care of personal
needs, such as trips to the rest room and drinking fountain. The table below
Personal Allowance Considerations
Personal allowance
documentation should
document:
Considerations Typical
Percentage
Allowance
A Basic Allowance which
considers the breaks available
for work during an 8-hour day.
Most firms allow, at least, two 10-minute
breaks during each 8-hour shift, the basic
personal allowance is 4.2 percent (20
minutes/480 minutes).
4.2
Normal office conditions 0.0
Normal shop, central heat, slightly dirty or
greasy.
1.0
Slightly disagreeable conditions. Exposed to
inclement weather part of the time, poor
heating, or poor cooling.
3.0
Extremely disagreeable conditions.
Proximity to hot objects, continuous
6.0
exposure to disagreeable odors and fumes, or
to excessive temperature ranges.
Total time allowed:
5 minutes 1.0
10 minutes 2.1
15 minutes
20 minutes
3.1
4.2
Any allowance for work
performed in a super-clean
room.
An additional allowance may be added to
consider the time require to assure that
super- clean room requirements are met.
4.0
Fatigue Allowance. A fatigue allowance considers the time required to recuperate from fatigue.
Fatigue Allowance Considerations
Personal allowance
documentation
should document:
Considerations Typical
Percentage
Allowance
Any allowance for
handling heavy
weights.
Effective Net
Pounds Percent of Time Under Load
Handled 1-12 13-25 26-50 51-75 76-100
1-10 0 1 2 3 4
11-20 1 3 5 7 10
21-30 2 4 9 13 17
31-40 3 6 13 19 25
41-50 5 9 17 25 34
51-60 6 11 22 x x
61-70 7 14 28 x x
71-80 8 17 34 x x
x – Study for possibilities for worker rotation and
other means to relieve fatigue.
Select
percentage
from table.
Multiply the table values above by the following
factors to consider lifting requirements:
For picking up from the floor, multiply the table
value by 1.10.
For placing the load above chest height, multiply
table value by 1.20.
For getting the load from chest height, multiply the
basic allowance by 0.50.
Depends on
work.
For sliding and rolling objects, multiply the weight
by the coefficient of friction to determine the
Depends on
work.
effective weight moved.
Coefficients of Friction (Average Values)
Surfaces Friction Coefficient
Wood on Wood 0.4
Wood on Metal 0.4
Metal on Metal 0.3
Sitting or standing. (Work will normally be less
tiresome if the position is varied frequently.)
0.0
Sitting. 1.0
Walking. 1.0
Standing. 2.0
Climbing or descending ramps, stairs, or ladder. 4.0
Working in close cramped quarters. 7.0
Any allowance for the
mental requirements
of the job.
Work largely committed to habit (e.g., simple
calculations on paper, reading easily understood
material, counting and recording, simple inspection
requiring attention but little discretion, or arranging
papers by letter or number).
0.0
Work requires full attention (e.g., copying numbers
or instructions, remembering part number while
checking a parts list, or filing papers by subject of
familiar nature.
2.0
Work requires concentrated attention (e.g., reading
of nonroutine instructions or cross-checking items).
4.0
Work requires deep concentration (e.g., making
swift mental calculations or memorizing items).
8.0
Any allowance for the
lighting on the job
site.
Continual glare on work area.
Work requiring constant change of light.
Less than 75 foot candle power on work surface for
normal work.
Less than 125 foot candle power on work surface
for close work.
2.0
Any allowance for
noise on the job site.
Constant, rather loud noises over 60 decibels (e.g.,
machine shops or motor test shops).
1.0
Average constant noises, level but with loud, sharp,
intermittent, or staccato noise (e.g., nearby riveters
or punch presses).
2.0
0.00 to 0.20 minute cycles 4.0
0.21 to 0.40 minute cycles 3.0
0.41 to 0.80 minute cycles 2.0
0.81 to 2.50 minute cycles 1.0
2.51 minutes or more 0.0
Any allowance for the
use of safety devices
or clothing.
No allowance should be made here unless it is
necessary to remove the equipment occasionally
for relief or if wearing the item causes fatigue.
Face shield 2.0
Rubber boots 2.0
Goggles or welding mask 3.0
Tight, heavy protective clothing 4.0
Filter mask 5.0
Safety glasses 0.0
Delay Allowance. A delay allowance covers unavoidable, predictable and unpredictable delays
for such activities as replenishing materials, rejecting nonstandard parts, making minor
equipment repairs, and receiving instructions.
Delay Allowance Considerations
Personal allowance
documentation
should document:
Considerations Typical
Percentage
Allowance
Basic Allowance Isolated job. Little coordination with adjacent jobs. 1.0
Fairly close coordination with adjacent jobs. 2.0
Worker moves once each 5 minutes. 5.0
Worker moves once each 30 minutes. 3.0
Worker moves once each 60 minutes. 2.0
Worker moves once each 2 hours. 0.0
Special Allowances . Any proposed special allowance must be supported by detailed
engineering analysis. An appropriate study should be conducted in each shop or functional area
to ascertain any requirement for a separate delay allowance. The analyst should assure that there
is no duplication between cycle time elements and allowance elements and that the Special
Allowance does not become a dumping ground for operation activity that is not an integral part
of shop work load.
⢠Work elements such as cleaning chips from equipment, tool care, or tool replacement,
though occurring irregularly, should be measured and the time required prorated directly
to the machine operating portion of the work cycle rather than as an allowance.
⢠Certain other irregularly occurring elements having a direct relationship to the job such as
obtaining parts and materials and periodic inspection should be added to the cycle time
on a prorated basis or as a separate work element rather than added as an allowance.
When a special allowance is appropriate, the time required is first calculated in minutes and then
converted to a percentage. The base for calculating and applying the allowance percentage is
normally the sum of the leveled time and the PF&D allowance. Appropriate special allowances
typically fall into two categories:
⢠Those that consider elements that occur on an unforeseeable basis:
o Power failures of nonreportable duration.
o Minor repairs to defective parts.
o Waiting for a job assignment.
o Obtaining job information from a supervisor, inspector, or production control
specialist.
o Unsuccessful hunt for parts or materials.
o Machine breakdown of nonreportable duration.
⢠Those that consider elements that occur periodically (daily, weekly, hourly) such as:
o Cleaning and lubricating equipment.
o Work area clean-up.
Applying an Allowance to Leveled Time . Allowances are normally expressed as a percentage of
standard time spent unproductively (e.g., a 15 percent PF&D Allowance indicates that 15 percent
of the worker’s standard time is spent unproductively). To apply an allowance, the analyst must
determine how much the leveled time must be increased to allow for the unproductive time. This
is accomplished by dividing the leveled time by the percentage of time spent productively.
Where:
T S = Standard time
T L = Leveled time
A PF&D = PF&D allowance in decimal form
For example: The leveled time for a particular task is 170 minutes, the PF&D Allowance is 15
percent, and there is no special allowance. The standard time would be calculated as:
Note: The leveled time is 85 percent of the standard time (85% of 200 is 170). The remaining 15
percent of the standard time (15% of 200 minutes is 30 minutes) is the allowance for personal,
fatigue, and delay factors.
8.3 – Measuring And Projecting Operation Efficiency
Comparing Labor Standard with the Actual Time . Standards represent goals for efficient
operation. Tasks are rarely completed in the allowed standard time. Work Measurement Systems
commonly use realization or efficiency factors to evaluate how the actual time required to
complete a task compares with the standard time for that task. Analysts can then use these
measures to identify tasks that require special analysis to identify and correct inefficient
operations.
Since estimators strive to estimate realistic contract costs, they use realization or efficiency
factors with labor standards to estimate future labor hours required to complete the task.
Calculating a Realization Factor . A realization factor is generally a measure of overall
performance (e.g., shop, product line, or plant). It will normally be calculated from historical
data as:
Where:
F R = Realization factor
T A = Acutal time to perform the work
T S = Standard hours for the task
R = Repetitions of the task included in the work
Don’t be confused by the fact that some firms refer to this calculation as an efficiency factor.
For example: A task has a standard time of 1.5 hours. Actual time to perform the task 100 times
is 300 hours. Using the model at ***, the realization factor would be 2.00
In the above example, actual experience shows that the work takes twice as many hours as the
standard time indicates.
Developing an Estimate Using a Realization Factor . The estimator can use the standard time
and realization factor to develop a realistic labor-hour estimate using the model at ***.
For example. An estimate of the actual time to complete the task above for 50 units would be
calculated as:
Y = T S x R x F R
= 1.5 x 50 x 2.00
= 150 labor hours
Where:
Y = Estimated hours
All other symbols are as defined above
Calculating an Efficiency Factor . An efficiency factor is calculated to demonstrate efficiency
against the standard (e.g., a task with an efficiency factor of .60 is being performed at 60 percent
efficiency). The factor is normally calculated:
Where:
F E = Efficiency factor
All other symbols are as defined above
For example. A task has a standard of 1.8 hours. Actual time to perform the task 100 times is
400 hours. The efficiency factor would be calculated as follows:
Developing an Estimate Using an Efficiency Factor . The estimator can use the standard time
and efficiency factor to develop a realistic labor-hour estimate.
For example. An estimate of the time to complete the task above for 50 units would be
calculated as:
Analyzing Realization and Efficiency Factors . Analysis of labor estimates developed using labor
standards requires extensive knowledge and experience. Even skilled industrial engineers
typically require special training in work measurement analysis. As a result, you should normally
request technical support whenever an offeror estimates labor hours using labor standards.
For each standard, offerors should be required to provide information on internal analyses of the
variance between the actual time required to complete the work and the standard time to
determine the causes for the variance and identify ways of managing performance improvement.
You should expect offeror’s to demonstrate continued improvement in realization and efficiency
factors. The figure below depicts some of the reasons for that improvement.
⢠At Unit #1, total labor-hours include substantial inefficiencies related to technical,
logistics, learning, and other factors.
⢠As production increases, there should be reductions in all areas of inefficiency. In most
cases, there should also be an improvement in the labor standard itself, as better
production methods are identified and implemented.
⢠By Unit #1000, the contractor should be operating efficiently, with only minor
inefficiencies related to such factors as unavoidable parts shortages.
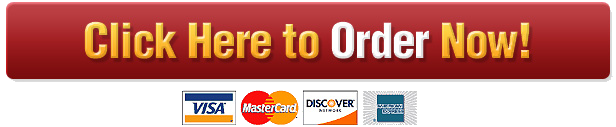
Is this question part of your Assignment?
We can help
Our aim is to help you get A+ grades on your Coursework.
We handle assignments in a multiplicity of subject areas including Admission Essays, General Essays, Case Studies, Coursework, Dissertations, Editing, Research Papers, and Research proposals
Header Button Label: Get Started NowGet Started Header Button Label: View writing samplesView writing samples